Primarily, brake friction formulations over the past several years have been preoccupied with the elimination of harmful components, chiefly asbestos and copper. But looking ahead, OE product designers are focusing their attention on reducing particulate emissions, as well as EV-specific developments.
That’s according to Holger Schaus, Tenneco’s vice-president of global engineering, OE braking.
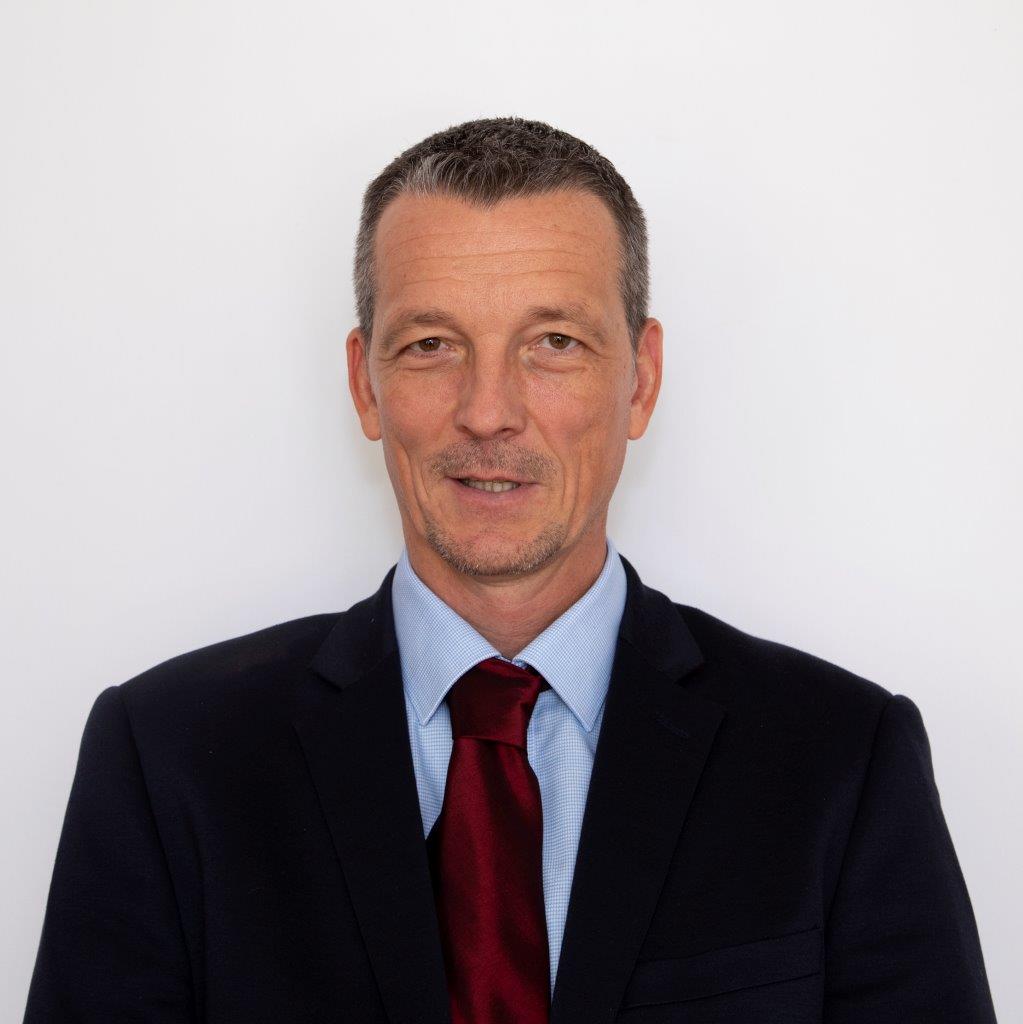
Speaking during a media conference to mark the 125th anniversary of Tenneco’s Ferodo brake brand, Schaus said the roots of the trend come from the European regulatory environment.
“For sure, this is Europe-centric first,” he said, referring to Euro 7, the pending OEM emission reduction standard for braking systems.
While Euro 7 standards are not in place yet, Schaus says OEMs have already been at work for several years, looking for ways to reduce emissions.
“Definitely there’s different maturity levels,” with the OEMs focusing on all these different criteria, Schaus said. Up till now, the focus has generally been on NVH, but now it’s concern for brake emissions (i.e., particulates) being released into the environment. “China is starting to build to the legislation [standards]. In North America to date, I think they’re monitoring, and I believe will assess the braking systems which are in place today.”
He says that the basic design concepts of North American brake systems, which favour rotor longevity over pad wear (a tendency which, Schaus says, is not viewed the same way in Europe), aren’t very compatible with the drive toward lower particulate emissions.
“So this is the focus area. Our focus is really to be a solution provider, on the product level as well as on the testing level, to serve our global customers.”
He adds that the focus on EV-specific designs is a key driver for industry in general, and Ferodo in particular. He points out that the focus on NVH seems obvious, due to the typical low noise level of EVs. But the challenges to brakes engineers nowadays go much further than that. For one thing, pad wear can be minimized (to reduce particulate shedding), but must still provide good initial “bite,” even after long periods of little or no use.
“The focus of our development is to offer good ‘cleanability,’ even in initial braking stops, and keeping a good NVH performance,” since with electrical and hybrid vehicles, engine noise is much reduced or non-existent, making NVH that much more noticeable. “So the focus is on these criteria – NVH, corrosion, and cleanability – while keeping the rest of the performance attributes.”
Recently, Ferodo introduced copper-free hybrid friction material composites, which simultaneously serve braking performance and comfort requirements in both internal combustion engine (ICE) and electric vehicles (EVs). This hybrid friction material combines the advantages of low steel (LS) and non-asbestos organic (NAO) composites in one concept for brake pads.
“So we have the stretch, where pad wear is very long, because of the regenerative ability of [EVs], but you need to still have the friction performance available, because of the high inertia and high ability of acceleration of these cars. So, in that context, we developed the hybrid friction material to comply with the stretch targets of NVH, corrosion and [continued] high performance.”
0 Comments